What is Failure Reason Analysis (FRA)?
Failure Reason Analysis (FRA) is a systematic approach used by organizations to investigate and understand the underlying causes of equipment failures, downtime events, or process deviations. The primary goal of FRA is to identify the root causes of failures and implement corrective actions to prevent their recurrence in the future. FRA involves analyzing various factors that contribute to failures, including equipment malfunctions, human error, environmental conditions, and process inefficiencies.
FRA typically begins with the collection of relevant data related to the failure event, such as equipment performance data, maintenance records, operator logs, and process parameters. This data is then analyzed to identify patterns, trends, and anomalies that may indicate potential root causes of the failure.
Once potential causes are identified, FRA teams use a variety of tools and techniques, such as root cause analysis (RCA), Pareto analysis, fishbone diagrams, failure modes and effects analysis (FMEA), and statistical process control (SPC), to further investigate and validate the root causes. By systematically analyzing the contributing factors and identifying the underlying causes of failures, organizations can develop effective corrective actions and preventive measures to address them.
Overall, Failure Reason Analysis is a proactive approach to failure management that helps organizations improve equipment reliability, minimize downtime, enhance operational efficiency, and ultimately optimize their overall performance.
Process of Failure Reasons Analysis (FRA)
Failure Reasons Analysis (FRA) is a systematic process used by manufacturers to identify and analyze the root causes of equipment failures or downtime events. The goal of FRA is to understand why failures occurred, determine the contributing factors, and develop effective strategies to prevent similar issues in the future. The process typically involves several key steps:
- Data Collection: The first step in FRA is to gather relevant data related to the failure event. This may include equipment logs, maintenance records, sensor data, production reports, and operator observations. Collecting comprehensive data ensures that all relevant information is available for analysis.
- Problem Definition: Once the data is collected, the next step is to define the problem or failure event. This involves clearly identifying the equipment that failed, the nature of the failure (e.g., breakdown, malfunction, downtime), and the impact on production or operations.
- Root Cause Analysis: Root cause analysis (RCA) is a critical component of FRA, focusing on identifying the underlying factors that contributed to the failure. RCA techniques such as the "5 Whys" or fishbone diagrams are commonly used to systematically investigate the sequence of events leading up to the failure and uncover the primary causes.
- Data Analysis: After identifying potential root causes, the collected data is analyzed to validate hypotheses and determine the most probable causes of the failure. This may involve statistical analysis, trend analysis, or comparison with historical data to identify patterns or correlations.
- Action Plan Development: Based on the findings of the analysis, an action plan is developed to address the root causes and prevent future failures. This may include implementing corrective actions such as equipment repairs, process improvements, maintenance schedule adjustments, or operator training programs.
- Implementation and Monitoring: Once the action plan is developed, it is implemented according to the defined timeline and priorities. Throughout the implementation process, ongoing monitoring and evaluation are essential to ensure that the corrective actions are effective and that the desired improvements are achieved.
- Continuous Improvement: FRA is an iterative process, and continuous improvement is essential to prevent recurring failures and optimize equipment reliability. Manufacturers should regularly review and update their FRA processes based on lessons learned, feedback from stakeholders, and changes in operating conditions or technology. By continually refining their approach to failure analysis, manufacturers can enhance their ability to identify and address potential issues, ultimately improving overall operational performance and efficiency.
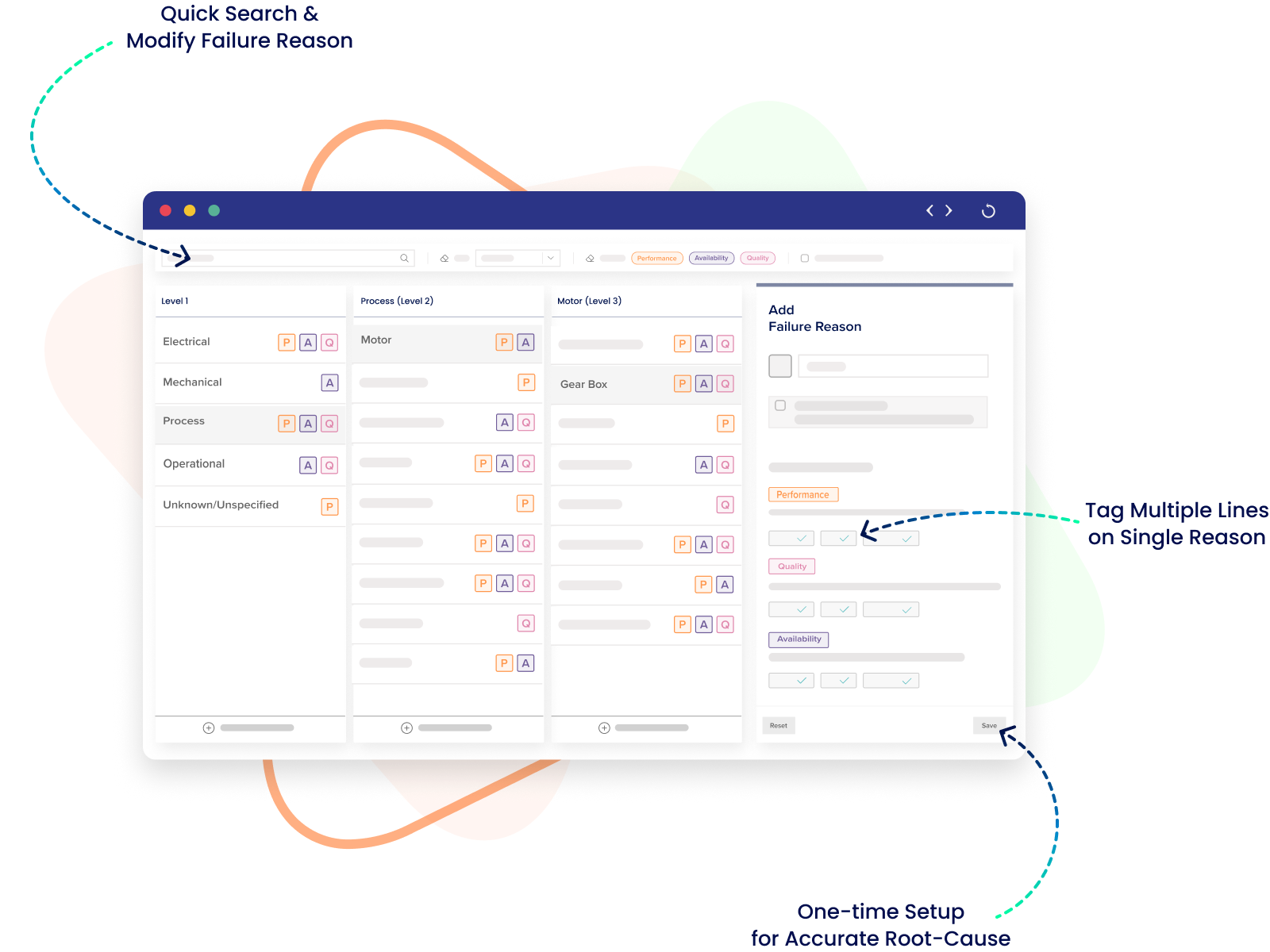
Add Failure Reasons in Modern MES
How do MES and FRA work together to improve performance?
Manufacturing Execution Systems (MES) and Failure Reasons Analysis (FRA) complement each other to enhance performance by providing valuable insights into production processes and equipment reliability. MES serves as a comprehensive software solution that collects, analyzes, and presents real-time data from various sources across the manufacturing environment. It enables manufacturers to monitor key performance indicators (KPIs), track production activities, manage resources, and optimize workflows. MES systems capture a wealth of operational data, including equipment utilization, cycle times, production rates, quality metrics, and downtime events.
FRA works hand in hand with MES to delve deeper into the root causes of equipment failures and downtime events. By leveraging the wealth of data collected by MES, FRA enables manufacturers to conduct thorough analyses of failure events and identify underlying issues that may be impacting performance. FRA techniques such as root cause analysis (RCA) help manufacturers pinpoint the specific factors contributing to failures, whether they are related to equipment malfunctions, process deviations, maintenance issues, or operator errors. By integrating FRA insights with MES data, manufacturers can develop targeted strategies to address root causes and implement preventive measures to mitigate future failures. This synergy between MES and FRA empowers manufacturers to proactively manage performance, minimize downtime, and optimize production efficiency.
Failure Reason Analysis(FRA) strategies and techniques
Failure Reason Analysis (FRA) employs various strategies and techniques to identify and address the root causes of equipment failures and downtime events. Some of the key strategies and techniques used in FRA include:
- Root Cause Analysis (RCA): RCA is a systematic process for identifying the underlying causes of problems or failures. It involves analyzing the sequence of events leading up to the failure and identifying contributing factors such as equipment malfunctions, process deviations, human error, or environmental factors.
- Pareto Analysis: Pareto analysis is a statistical technique used to prioritize problems or issues based on their frequency or impact. In the context of FRA, Pareto analysis helps identify the most common or significant causes of equipment failures and prioritize them for further investigation and corrective action.
- Fishbone Diagram (Ishikawa Diagram): A fishbone diagram is a visual tool used to identify potential causes of a problem or failure. It categorizes potential causes into different categories such as equipment, processes, people, materials, and environment, allowing teams to systematically explore all possible contributors to the failure.
- Failure Modes and Effects Analysis (FMEA): FMEA is a proactive technique used to identify and prioritize potential failure modes of equipment or processes and their potential effects on operations. It involves assessing the severity, likelihood, and detectability of each failure mode and developing preventive or corrective actions to mitigate risks.
- Statistical Process Control (SPC): SPC involves monitoring and controlling production processes using statistical techniques to detect and prevent deviations or abnormalities that could lead to failures. By analyzing process data in real-time, SPC helps identify trends, patterns, or anomalies that may indicate impending failures.
- Reliability Centered Maintenance (RCM): RCM is a maintenance strategy focused on optimizing the reliability and performance of equipment by identifying and prioritizing maintenance tasks based on the criticality of assets and their failure modes. RCM aims to minimize downtime and maximize asset availability by implementing the most effective maintenance strategies for each asset.
These FRA strategies and techniques empower manufacturers to systematically analyze equipment failures, identify root causes, and implement targeted corrective actions to improve reliability, minimize downtime, and optimize operational performance. By leveraging these tools, manufacturers can proactively manage their assets, enhance productivity, and achieve their operational objectives.
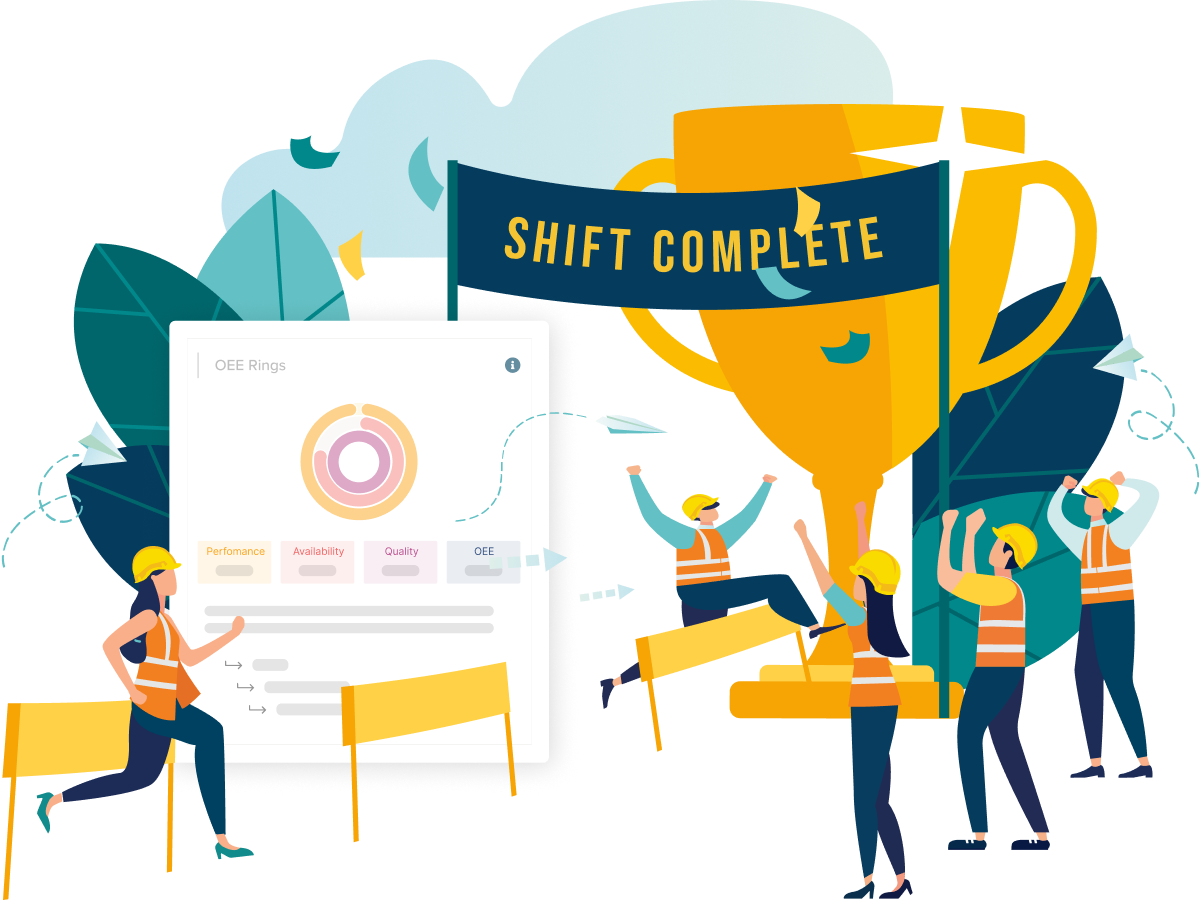
Shift complete success
Conclusion
Failure reasons analysis and manufacturing execution systems are powerful tools that can improve performance while maintaining quality standards. Empowering the workforce with these technologies allows workers to take control of their own work and make decisions that will improve productivity while reducing errors.